Ammunition fabrication for Nellis Air Force Base | August 2020 - September 2021
We were contracted by a U.S. Air Force base in Las Vegas to fabricate eight full-scale munition replicas for training purposes.
After visiting the base to gather detailed measurements, we created accurate 3D models and produced the replicas using 3D printing, plywood, and CNC parts.
We have built a custom spray booth and applied automotive spray painting techniques to achieve realistic finishes.


















Vegas Fighting Covid | April 2020 - July 2020
In early 2020, I co-organized Vegas Fighting Covid, a grassroots effort formed to support our local medical community during a time when personal protective equipment (PPE) was in short supply. What began with just a few of us quickly grew into a coordinated team of dozens of 3D printers, volunteers, and local businesses all working together to design, manufacture, and donate PPE to frontline workers.
Inspired by the SmarterEveryDay YouTube channel, we used shared open-source designs and tools to produce critical gear. Over the course of the initiative, we successfully donated 1,734 face shields and over 4,000 ear savers to 51 medical facilities across the region.

Golden Knight Helmet | July 2018
During the Vegas Golden Knights’ debut season and historic run to the NHL finals, we were commissioned to create a giant helmet for the Caesars Palace statue to show citywide support. With just one week and one shot to get it right, we prototyped small-scale versions to iron out challenges.
The final piece was built from foam, vinyl-wrapped, and installed just in time for the finals — a bold, fast-turnaround project that brought together design, fabrication, and team spirit.

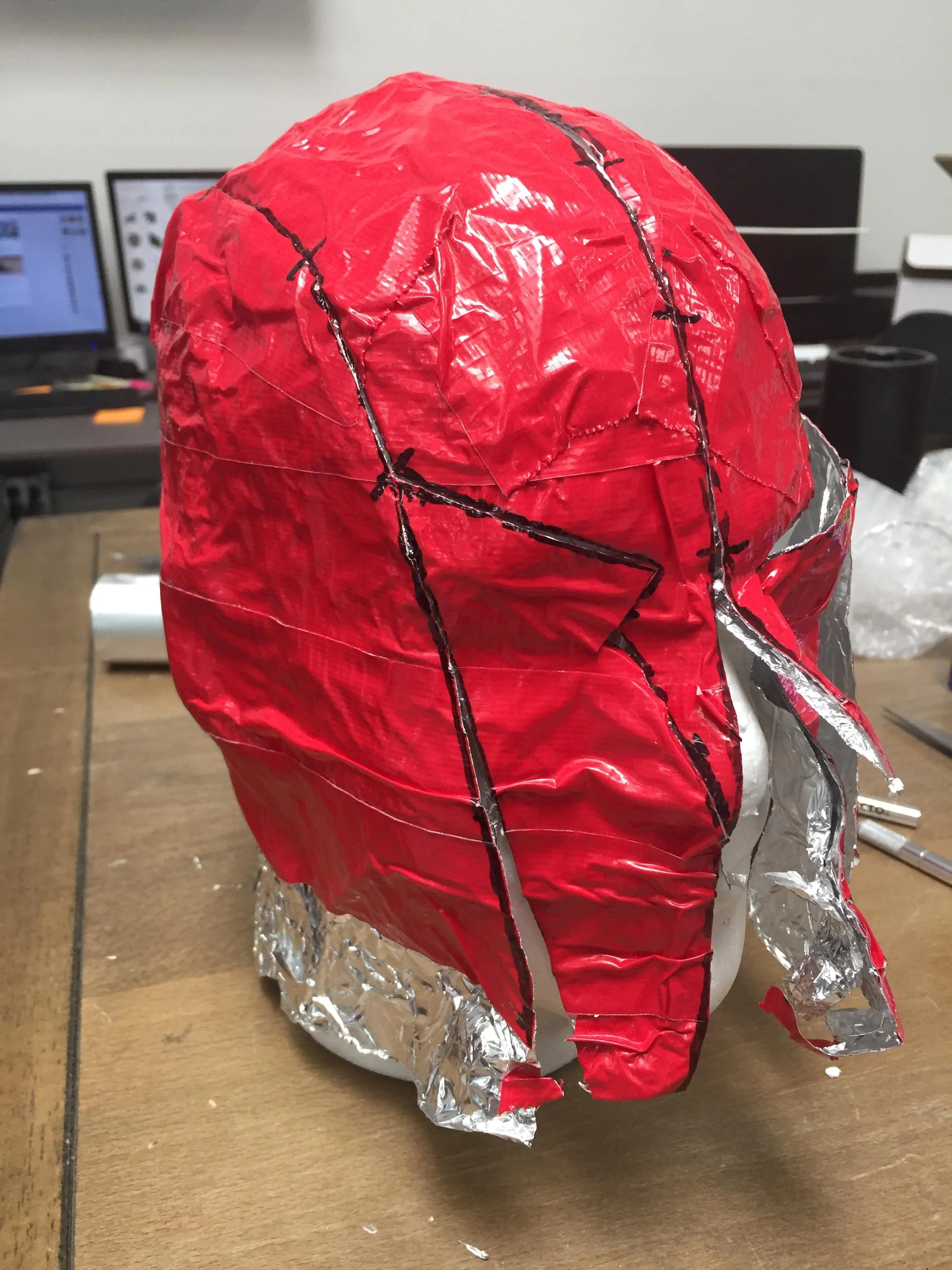











Nevada State Museum Donation Box | February 2018
We partnered with UNLV’s engineering department to create a custom donation box for the Nevada State Museum. Our role was to design, 3D model, and print a scaled ichthyosaur fossil, while the UNLV team engineered the housing structure to display it.
The project took 3 months, including over 250 hours of 3D printing and 200 hours of post-processing, using a mix of PLA and resin. The finished piece now lives at the museum as a functional and educational exhibit, encouraging visitors to support its mission.

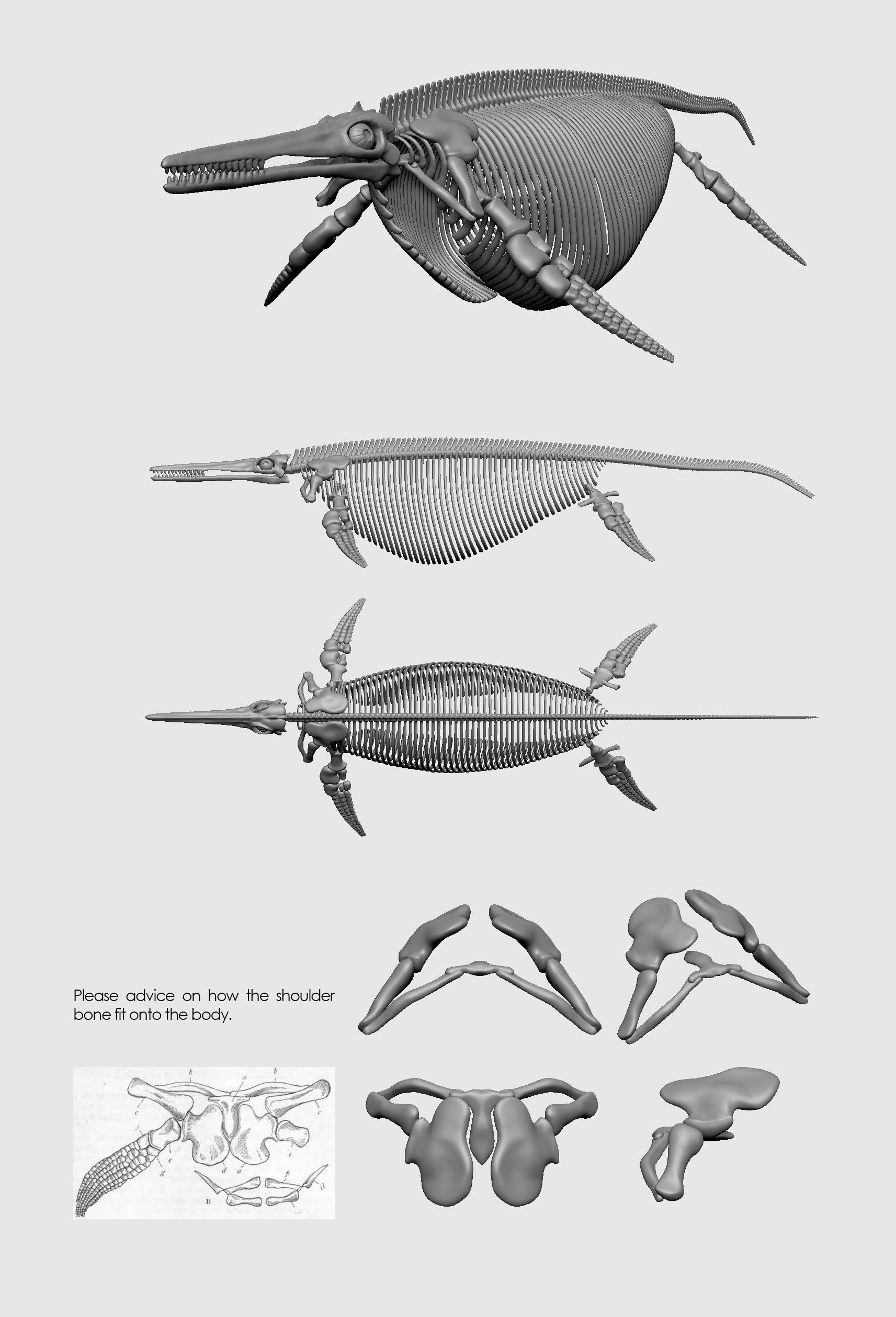










